Electrical insulation should be in the best possible shape when new, but there are still many things which can result in the failure of electrical insulation including the likes of electrical stress, vibration, dirt, corrosive vapours, excess humidity or moisture, mechanical damage and extreme temperatures.

There are a number of different components that make up electrical insulation, which have all been chosen in order to be able to withstand the very different electrical, thermal, environmental and mechanical stresses that take place in different areas of the structure. IR testers, like those found at RS Components, can help test insulation.
The length of time in which electrical insulation will last before it begins to fail will be dependent on how those individual components are arranged, how they contribute to the system’s mechanical and electrical integrity, and the manufacturing process that was used to create them. However other factors can also have a major influence on the length of the service life of electrical insulation.

Causes of electrical insulation failure
Temperature
Even the smallest change in temperature can result in a big decrease in insulation resistance. There is no uniformity to the current distribution with a given insulation, so more current is carried by the weakest part of the insulation, causing it to heat up quicker than some other areas. The temperature will stay the same so long as the insulation is able to conduct the heat away as quickly as it has been generated, but if not the insulation’s weak spots will grow hotter and hotter until thermal breakdown begins.
Electrical stresses
Electrical equipment is frequently subject to current and voltage surges that are either generated externally or from within. A voltage surge caused by lightning or the switching of a big inductive load can cause insulation to physically rupture, with molecular bonds destroyed. Electrical stresses gain higher significance with apparatus that is exposed to voltage transients or with high-voltage equipment.

Environmental
Environmental factors such as acids, alkalis, chemicals, dirt, moisture and oils can start to degrade electrical insulation over time. Moisture that absorbs into insulation begins to decrease insulation resistance, penetrating its pores and cracks and creating low resistance paths that enable creepage currents and other possible dielectric failure causes. Insulation is directly attacked by chemical fumes like alkalis and acids, which are often found in industrial business environments, permanently lowering insulation resistance. Interior insulation surfaces can be covered by oil films, cutting down on its heat dissipating abilities and promoting thermal flagging, resulting in eventual failure.
When combined with moisture, dirt and dust can become conductive, resulting in creepage currents and the degradation of insulation in addition to the reduction of the insulation’s ability to dissipate heat.
The length of life of a piece of equipment is often highly dependent on the insulation being capable of excluding chemicals, dirt, moisture and oxygen. It is important to conduct regular checks on the functionality of electrical insulation, which can be done with the help of an IR tester, which is able to detect problems before insulation fails completely.
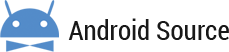